News
Don't miss out on what's happening at Richard Burbidge, plus lots of guides and tips for successful home renovations.
Following the success of our PaintReady Stairparts range, we have created a new collection of ready-primed wall panelling kits designed to deliver faster and smoother finishes for interior design projects. Wall panelling is currently experiencing a comeback. An interior design style that is low-cost, easy to install and offers soundproofing and insulation benefits, panelling is a home improvement trend that is not looking to stop any time soon. For time-efficient and cost-effective DIY solutions, our PaintReady kits arrive ready for fitting, with no sanding, filling or priming needed, achieving a smoother, faster finish, streamlining the renovation process and expediting installations. Our accessible kits make creating a stylish home easy and with a 20% rise in women DIYers*, we pride ourselves on creating products that inspire design, mix style with functionality and are easy to use. Whether you are a seasoned craftswoman or a DIY novice, our kits make achieving your desired look simpler than ever. The collection features four distinctive wall panelling kits, significantly expanding design possibilities and DIY projects. Within these kits, versatile squares, elongated rectangles, and half-wall variations provide endless creative opportunities for homeowners to install easily. Users can experiment with various kit combinations to achieve the desired look, designed to allow you to effortlessly blend different kits and create a unique aesthetic ranging from traditional to contemporary or even eccentric styles. The high-quality mouldings are precisely cut and mitred to size, then coated with our new water-based primer, providing an ideal surface for paint application and final finishing. With sustainability in mind, we use FSC certified pine, offering eco-friendly design solutions. To view our complete PaintReady panelling kit collection, click here. *Source: https://www.economist.com/podcasts/2024/01/04/sisters-are-doing-it-for-themselves
READ ARTICLETransforming your garden into a stylish and functional outdoor oasis doesn't have to break the bank. Here at Richard Burbidge, we’re embracing the rising trend of creating distinct ‘zones’ within outdoor spaces. This trend allows you to maximise every inch of your outdoor area by designating specific areas for different activities, whether it's dining under the stars, unwinding in a cosy lounge, or immersing yourself amongst some greenery. By defining these zones, you not only enhance the functionality of your garden but also elevate its aesthetic appeal, creating a seamless blend of practicality and style. Dining Zone Enhance your outdoor dining experience by adding a cosy dining zone to your garden. With a wide selection of metal, glass, or timber balustrades available here at Richard Burbidge, you can define your area and create a sense of separation from the rest of the garden. Complete the look with budget-friendly outdoor furniture and string lights for a warm and inviting space ready for dining in the summer months. Lounge Zone Create a relaxing lounge zone where you can unwind and enjoy the outdoors with the use of our metal or glass balustrades to help enclose the space and add privacy. Incorporate comfortable seating options like lounge chairs or outdoor sofas and accessorise with cushions and throws for added comfort. You could even consider adding a fire pit or outdoor heater to keep your space feeling cosier for longer. Nature Zone Bring a touch of nature to your garden by creating a greenery zone with potted plants and garden accessories. Introducing timber decking accessories is a great method to elevate your outdoor area. By incorporating decking panels like our crosshatch or sunburst designs, you can enhance your gardens charm and usability, keeping that natural feel while crafting a warm and inviting space. Metal decking Accessories Alternatively, metal decking accessories offer a sturdy and industrial vibe, helping create a practical and sleek look. Choose from our budget-friendly options like metal railings, balusters, and post caps to define your decking space. Not only are these accessories easy to install, but they also don’t require much maintenance, making them an ideal choice if you don’t want to spend too much time on their upkeep. Glass Decking Accessories For those who want a more contemporary and sophisticated look, glass decking accessories offer a great alternative. Glass panels or balustrades can create a sense of openness while maintaining safety. Upgrading your garden on a budget is easy with the right accessories and a bit of creativity. Whether you prefer the durability of metal, the sleekness of glass, or the natural look and feel of timber, we have plenty of options for to suit every budget. By incorporating decking accessories into your garden design and embracing the trend for creating "zones," you can transform your outdoor space into a stylish and functional oasis that you'll love spending time in. View our full decking range here
READ ARTICLEHere at Richard Burbidge, through our latest sustainability report, we have taken the time to analyse where our carbon footprint comes from to ensure we continue to deliver on our sustainable promises. The rising threat of greenwashing across competing industries has made it hugely important for us to document regular updates on our sustainability achievements. This is especially vital as we progress further with our pledges to achieve Net Zero, as part of the United Nations Race to Zero campaign, by no later than 2050 and halve our greenhouse gas emissions before 2030. We are committed to delivering the most eco-friendly and sustainable selection of timber products, with a focus on forming eco-friendly initiatives to positively impact the climate and contribute to a better planet and society. Here are some of our most recent achievements: Reduced our Scope 1 & 2 carbon emissions by 62% compared to our baseline year. Installed 2,600 solar panels at our North Wales factory, generating 40% of the site's total energy requirements and contributing to carbon emissions reduction. Upgraded our Forklift Truck fleet from 30 diesel/LPG trucks to 20, with 19 now being zero-emissions electric trucks and one remaining diesel-powered. Transitioned to cardboard packaging solutions for all flooring items in the Atkinson & Kirby product range in 2023. Identified packaging changes for the Richard Burbidge product range, with implementation scheduled throughout 2024. Installed seven electric vehicle charging points at our HQ car park. Engaged with 15 global suppliers, comprising 80% of total company spend, to present our sustainability report and updated Archwood collaboration document. Communicated policy changes impacting suppliers, a crucial step in achieving our sustainability goals Reflecting on the past year, our Manager Director, Josh Burbidge, describes how the business is setting the benchmark with Net Zero goals and year-on-year transparency towards our sustainability progress: “At Richard Burbidge, we’re passionate about design, manufacturing and the sustainable sourcing of timber products. We have made great progress on our Net Zero journey, reducing our Scope 1 & 2 carbon emissions by 62% versus our baseline year. This is a fantastic achievement but there is still much more work to be done. We have prepared the report to update on our journey so far and highlight what we will be focusing on in the coming years’. Download the full Sustainability Report 2023 here.
READ ARTICLESelf-build home and garden influencer, Kate Clarkson, has recently decorated her new home in Yorkshire. As it was a self-build, the project involved interior designing the whole house. One thing she wanted to do was create a sophisticated space that felt stylish yet lived-in for her family. This included beading and panelling in numerous rooms throughout her home, including the master bedroom, hall, stairs and landing, WC, family bathroom, and one of her daughter’s bedrooms. With a desire for a classic aesthetic, Kate selected distinct panelling styles for the various rooms, tailoring her choices based on size and scale. Collaborating closely with her joiner, Kate mapped out precise dimensions and spacing to ensure the overall look was subtle but striking. With her joiner's help, she attached the chosen beading and mouldings, using caulk, then paint to really bring the rooms to life. What were once one-dimensional rooms were transformed into traditionally sophisticated spaces with added textures and undeniable character. The painted wall panelling in the master bedroom adds depth to the space and allows the master bed to become the main focal point of the room. The added details of the archway and light oak furnishings ensure the room maintains a homely feel amongst this eye-catching feature. To complement Kate's vision, several of Richard Burbidge’s decorative mouldings were employed to create what is a fully panelled Master Bedroom. To achieve this, Kate used Pine Decorative Panel Mouldings to enhance the architecture of the room. Using Farrow and Ball paint in the shade Slipper Satin, the moulding is brought to life. Continuing her cohesive design, Kate extended the use of Pine Decorative Panel Mouldings to the halls, stairs, and landing, this time opting for Farrow and Ball’s shade School House White, creating a unified and sophisticated look throughout her self-built Yorkshire home. For her Downstairs WC, Kate opted to add Pine Decorative Panel Mouldings to her walls, then coated them with Farrow and Ball paint in shade Wine Dark to create a rich and intimate space. In her family bathroom, Kate used Pine Decorative Panel Mouldings as her beading and Richard Burbidge’s Pine Dado Rail Mouldings to fashion a timeless and elegant wainscot wall panelling. Painted in Farrow and Ball's Terron, this choice perfectly complemented the white Plantation shutters and standalone bath. The wall panelling adds a traditional feel to this new build home that still feels contemporary. To view all of the Richard Burbidge mouldings used by Kate in her home, visit her Instagram reel here: https://www.instagram.com/reel/CysLh7wKeou/?utm_source=ig_web_copy_link View Richard Burbidge’s full collection of decorative mouldings here: https://richardburbidge.com/shop/mouldings
READ ARTICLEA rising trend with homeowners is the ability to paint timber to match colour palettes and interiors, as well as create statements. Timber staircases in particular offer a ‘blank canvas’ where a lick of paint can instantly add a ton of character. With this in mind, our Elements range, which was previously only available in Oak – which is an expensive timber to paint – is now officially launched in Pine. This alternative is a more budget-friendly option, making it a great solution for those looking to save on costs whilst still enjoying high-quality timber. By offering Pine drilled rails alongside the sleek metal balusters that are available in our Elements range in a variety of lengths, homeowners now have the perfect starting point for painting and matching staircases to the wider style of their home or hallway. Always created with easy installation and cost-effectiveness in mind, our balusters can easily slot into the pre-drilled rails and fix with a multi-purpose adhesive in a mastic gun. Perfect for home DIY, plus the option to paint our Pine rails allows for a more affordable staircase makeover. As part of our future plans here at Richard Burbidge, we’re listening to our customers and always analysing trends to ensure we focus on supplying the right products. That’s why we are increasing the manufacturing of our Pine rails for 2024, which will add to the abundance of innovative, new products which we have in development. To explore our Elements range, please visit the link below where you can request a design consultation from our trusted and knowledgeable team: https://richardburbidge.com/shop/stairparts/elements?_gl=1*m8212b*_up*MQ..&gclid=Cj0KCQjwma6TBhDIARIsAOKuANwZwkXah-kEyQq0sG0tO0O3Zq49ayok1p6nB5FsLi0ydZ7-Dk5gRM4aAieQEALw_wcB
READ ARTICLELeading manufacturers, Atkinson & Kirby and Richard Burbidge, partner with Manchester design house, BOBO1325, to launch a trend-led styling collection to promote timeless maximalism, sustainability and eco-conscious living spaces. With a shared commitment to sustainability and premium design, renowned hardwood flooring brand Atkinson & Kirby, along with its sister brand Richard Burbidge, the UK's leading supplier of stairparts, decorative mouldings, and decking accessories, have joined forces with BOBO1325. This award-winning design house, based in Manchester, will collaborate with them to launch a new Maximalism-inspired styling collection under the banner of 'Bold'. BOBO1325, founded by designer Beth Travers, is celebrated for its innovative maximalist wallpaper collections. Together, BOBO1325, Atkinson & Kirby and Richard Burbidge embark on a creative journey to inspire designers and homeowners to elevate their living spaces with bold, vibrant, and sustainable interior design. The brands are coming together to explore and promote the timeless trend of Maximalism in interior design. Their collaboration places a strong emphasis on creating sustainable and long-lasting living spaces, aligning with evolving attitudes towards design trends and their sustainability in the world of interior design. Atkinson & Kirby and Richard Burbidge believe that well-considered design plays a significant role in contributing to sustainability. This involves the incorporation of timeless design features achieved through the use of hard-wearing, locally sourced, high-quality materials. As part of this vision, the partnership introduces a series of captivating room designs aimed at inspiring interior designers to infuse their living spaces with colour, pattern, and joy while considering environmental, ecological, and longevity factors. Josh Burbidge, Managing Director of Archwood Group, comments, “Offering sustainable and responsibly sourced products is at the forefront of what we do. Combining this ethos with design conscious and trend-led collections is incredibly important to us, so BOBO1325 seemed like the perfect brand to partner with. “The hope of this collection is that it will help designers pick the perfect products for their projects. Our hardwood flooring, stairparts and mouldings can last many years, as many trends come and go. Partnering with BOBO1325 means customers can easily see what products match their home and give rooms a new lease of life in an eco-conscious way.” Both Archwood Group brands and BOBO1325 share a profound commitment to sustainability. Archwood actively participates in the United Nations Race to Zero campaign, dedicated to lowering global emissions. Meanwhile, BOBO1325 stands out for its intricate hand-drawn designs, meticulously crafted using sustainable materials and eco-friendly practices. These designs are brought to life just 20 miles from their Manchester-based studio, printed on FSC certified papers using eco inks. Expressing her enthusiasm, Beth Travers, BOBO1325 Founder, comments: “This is the perfect partnership to encourage customers to embrace mixing textures, patterns, and tones, naturally elevating their interior spaces and curating visually captivating designs that allow their style and personality to shine through. I'm enthusiastic about colour and pattern and hope that, together, the Archwood Group and I can inspire confidence sustainably.” For information about BOBO1325, please visit: https://bobo1325.com
READ ARTICLE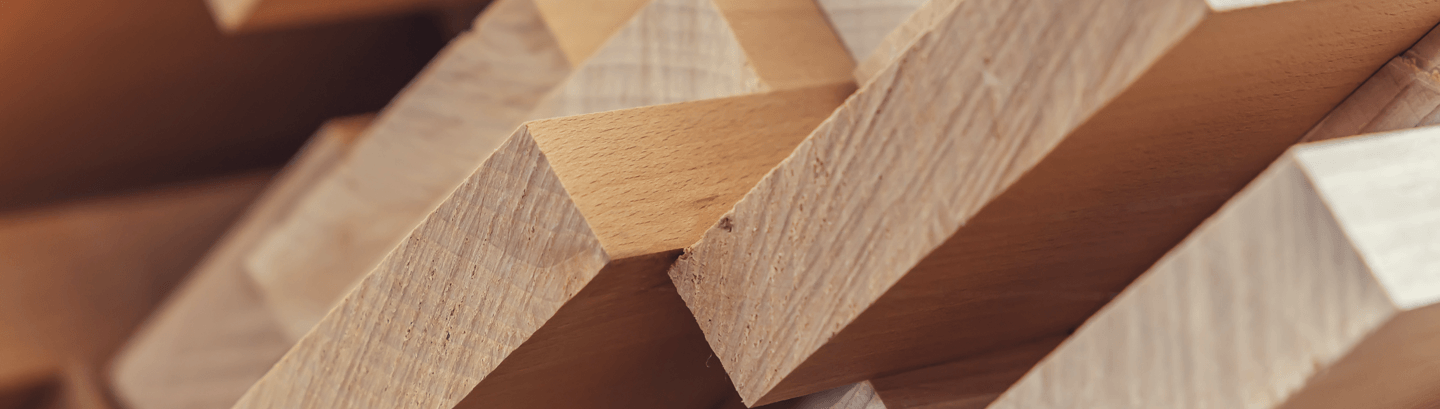
Combining fantastic design with the finest craftsmanship
Established in 1867, family run Richard Burbidge has been passionate about the design, manufacture and supply of timber products for over 150 years. Today we offer a range of innovative products designed to transform your home.
about us